Laser welding
Laser welding uses the energy of the laser as a heat source. Welding is done using a pulsed laser. In the process, the workpiece is positioned under the microscope. Depending on the material, damage and function of the workpiece, the appropriate filler metal in alloy and diameter is then selected. In most cases, the wire is fed by hand.
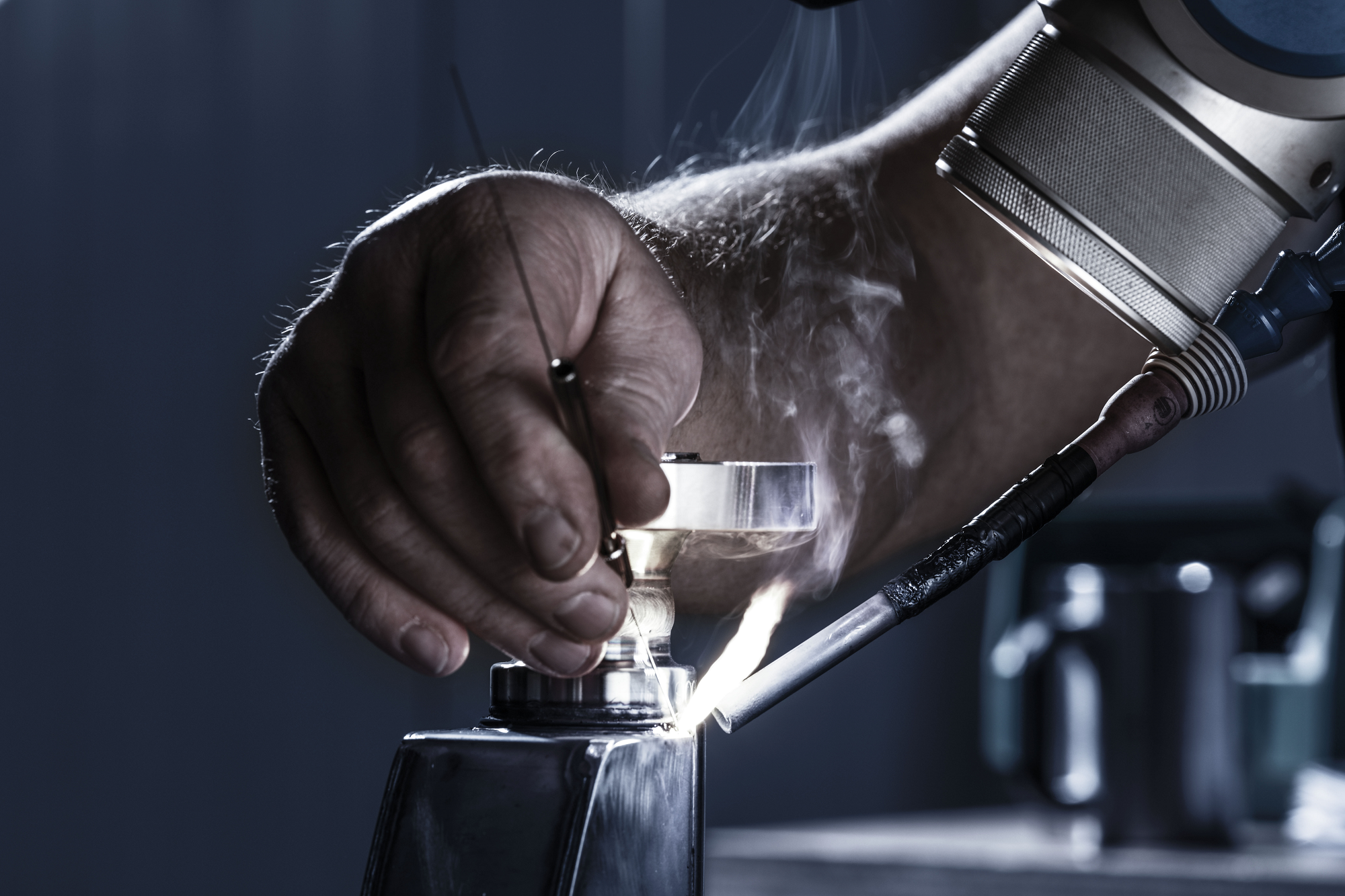
In the past, only pulsed lasers were used for manual repair welding.
So-called continuous wave (CW) or fibre lasers were only used in conjunction with CNC-controlled workpiece or beam guidance.
So-called continuous wave (CW) or fibre lasers were only used in conjunction with CNC-controlled workpiece or beam guidance.
Currently, systems up to 900 watts are available for manual and mobile repair welding.
In the processing parameters, the focus diameter on the workpiece surface, pulse power, pulse duration and pulse frequency are set as power-determining variables. The spot to be processed is now targeted with the help of the crosshairs in an eyepiece.
The filler material, usually in wire form, is then placed on the welding spot and the welding pulses melt the wire and the underlying base material. The laser welding wire and the workpiece thus form a bond.
In the processing parameters, the focus diameter on the workpiece surface, pulse power, pulse duration and pulse frequency are set as power-determining variables. The spot to be processed is now targeted with the help of the crosshairs in an eyepiece.
The filler material, usually in wire form, is then placed on the welding spot and the welding pulses melt the wire and the underlying base material. The laser welding wire and the workpiece thus form a bond.
Wire diameters from 0.1 mm to at least 1.2 mm can be homogeneously welded on and with different materials.
These include copper, titanium, aluminium and of course various steel alloys.
These include copper, titanium, aluminium and of course various steel alloys.
Advantages:
- precise work with pinpoint, accurate energy input
- welding of complicated seam geometries
- low heat influence, thus minimal structural change
- lower thermal distortion
- shrinkage-free weld seams
- less time required for reworking
- large working distance possible (welding up to approx. 500 mm distance or in hard-to-reach places)
Disadvantages:
- depending on the design, the welding systems are cost-intensive to purchase
- If filler metals are required, they are relatively expensive due to the small production quantities. However, this disadvantage is offset by the fact that only small quantities are applied relative to the welding time, and there may be no need for lengthy post-processing